Probing the vibrational response of structural components ― a process known as modal testing ― is important for their design and maintenance. Thanks to the efforts of Keio researchers, a modal testing setup with battery-free sensors and wireless communication has now been successfully demonstrated.
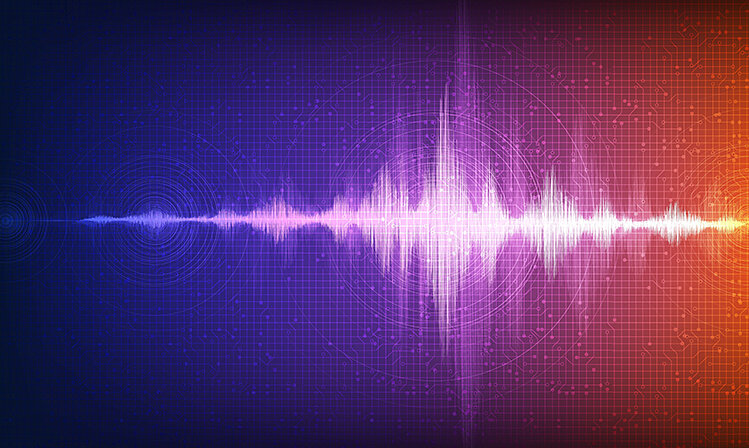
©︎ Varunyu― stock.adobe.com/jp
In engineering, the concept of modal testing is extremely important. It refers to obtaining information about the natural frequencies of vibrational modes that are inherent in a designed structure. A building, for example, will have intrinsic vibrational modes due to the way it is constructed. It is crucial that the frequencies of these modes do not coincide with possible earthquake frequencies, as then an earthquake could trigger vibrations with increasing amplitude through the principle of resonance, resulting in the building's collapse. (Resonance is the triggering of a vibration through the waves generated by another, nearby source of vibrations ― a guitar's strings for instance may start to vibrate because of the sounds produced by another instrument played in its vicinity.) Another example is the construction of bridges, the modes of which should not be triggerable by gusts of wind.
Modal testing is essential for the design and maintenance of structural and machine components; examples include car bodywork, aircraft parts, and wind turbines. Modal testing can be done by means of computer simulation, and also through actual experiments by attaching a 'shaker' to excite vibrations in the structure, together with sensors that pick up the relevant vibrational information. These sensors are usually accelerometers, devices that locally measure proper acceleration ― the rate of change in velocity ― which can be related to a vibrational frequency. Traditionally, the sensors have electric wires attached to them for signal transfer as well as powering the sensor. Typically, modal testing uses many accelerometer sensors; the weight of the required wiring is considerable and can disturb the testing accuracy, particularly in light-weight structures. The use of batteries for powering the accelerometers can also be problematic; in extreme environments, such as in the field of aerospace, replacing them is difficult. To overcome wire-weight and battery-replacement issues, Jin Mitsugi and colleagues at Keio University have developed a modal testing setup with wireless, battery-free sensors. The approach is expected to make modal testing more robust and more widely applicable.1
The main components of the sensors are a radio frequency integrated circuit (RFIC), used for receiving and transmitting radio signals, an antenna, and a micro-electromechanical accelerometer. A particular operational radio frequency is assigned to each of the sensors for RFIC communicas. A software-controlled device, known as an 'interrogator', regulates the frequency allocations and all further communication protocols. The sensors receive their electrical power wirelessly through the ultra-high frequency radio waves (in the 860 - 960 MHz range) emitted by the interrogator. Because the sensors scatter a part of the received radiation back, they are called "backscatter sensors."
Mitsugi and colleagues tested the performance of the setup for a long, thin stainless-steel bar, vibrationally excited by means of a shaker. Two regimes were examined. In the first (called sine sweep excitation), the shaker delivers one frequency at a given time, but the frequency changes over time. This test is mostly used when a specific frequency is of interest. In the other (called random excitation), many frequencies are excited at one given time. This regime is mostly applied for testing the general endurance of a structure, for example to check whether damage might occur during transportation of the structure.
The researchers compared the wireless test with the results obtained from a commercially available modal testing system (with wires). The random excitation regime results matched very well for vibrations up to 100 Hz.
Mitsugi and his colleagues conclude in their paper that the experiment reveals that "wireless modal testing up to 100 Hz can be successfully performed by battery-free wireless sensors." This research is an important proof-of-concept demonstration and will stimulate further research with the promise of making modal testing more versatile.
Published online 25 May 2023
About the researcher
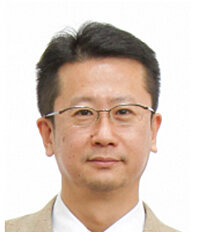
Jin Mitsugi ― Professor
Faculty of Environment and Information Studies
Jin Mitsugi received a B.S. from Nagoya University, and an M.S. and Ph.D.
from Tokyo University all in Aerospace Engineering
in 1985, 1986 and 1996, respectively. He is currently a Professor at
Faculty of Environment and Information Studies, Keio University.
His research interests are signal processing,
wireless communication, and computational mechanics.
Links
Reference
- Mitsugi, J. et al. Wireless Modal Testing with Multiple Battery-Free Backscatter Sensors. IEEE J. Radio Freq. Identif. 6, 299-306 (2022). | article