Unstabilizing vibrations in remotely controlled systems can be reduced using an elastic feedback method
Published online 25 February 2016
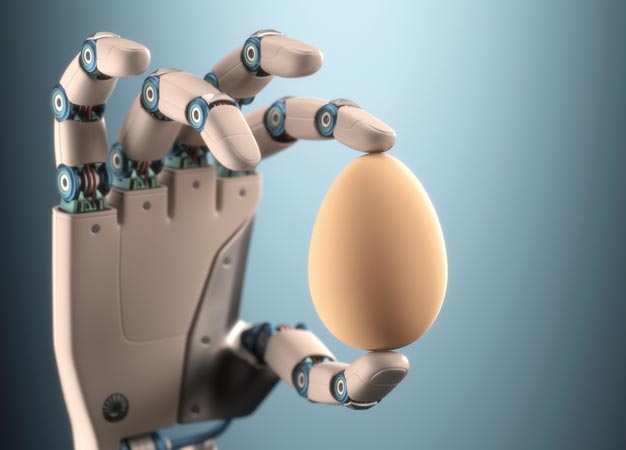
Improving the communication between remote mechanical systems and their human controllers can lead to more precise movements.
© ktsimage/iStock/Thinkstock
Remotely controlled devices offer a safe way to perform hazardous tasks, such as bomb disposal or activities in radioactive areas. Eiichi Saito and Seiichiro Katsura from Keio University's Department of System Design Engineering have developed a method for increasing the stability and precision of these remotely controlled systems1.
Remote-controlled robots in risky settings may need to grab an object firmly enough not to drop it, but not so tightly as to damage it. This balance is achieved through a concept known as feedback: the robot's movements are automatically adjusted based on measurements of the forces between the grabbing tool and the object. The same type of give-and-take is needed to direct robots to precise locations.
However, because the robot and its human controller are at different locations, there is a time delay between the input from the controller reaching the robot and the feedback reaching the controller. This time delay can make the system vibrate and become unstable.
The Keio team proposed a novel time-delay compensation scheme that models the system as a series of oscillating masses connected by springs. They introduced infinity-order equations to this mass-and-spring concept to predict vibrations across a wide range of frequencies. Since time delay is a type of infinite-order problem that works across all frequencies, using these equations in the algorithm that determines the feedback in their system helped to reduce the deleterious effects of the vibrations.
"From an engineering point of view, it is better to use a simple model, but high-speed adjustments in position lead to high-frequency vibrations," explains Katsura. "So there is a trade-off between simplicity in control design and suppression of these vibrations. We introduced so-called infinite-order modeling and control to solve the trade-off issue."
The researchers experimentally validated their approach in a simple mechanical system comprised of a computer-controlled motor that moves an object to a desired position. This system was then controlled by a second computer that acted as the remote controller. A time delay of 25 milliseconds was artificially added between the two computers. The team first tested a common alternative approach for reducing the negative effects of time delays known as the Smith predictor. This alternative method achieved a steady final position, but fell almost a millimeter short of the intended target. Saito and Katsura's method reached the steady end state in the same time but with a higher accuracy.
"At present, the system only considers a position-control system," says Katsura. "In future work, we hope to extend this to force-control systems too."
Reference
- Saito, E. & Katsura, S. Time delay compensation using equivalent elastic force feedback. IEEJ Journal of Industry Applications 4, 688-695 (2015). | article